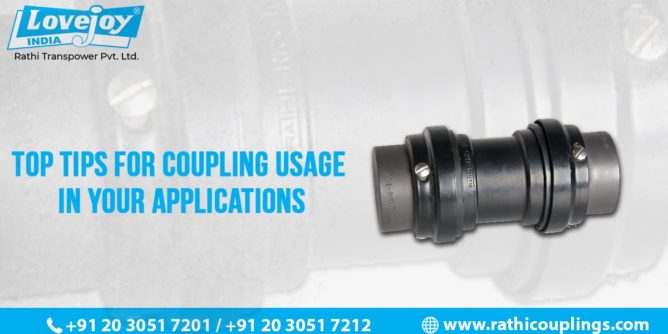
Picking the right coupling for the task that needs to be done means asking the right questions before indicating a specific style. Choices abound, and more than one coupling type might be appropriate for some given application. Here we present master tips and tactics.
Try not to pick coupling based on habit or cost alone
Picking a coupling type is frequently a matter of having chosen that equivalent type for a previous project. However, on the grounds that not all couplings are made equivalent, indicating out of familiarity often mismatches needs with coupling capabilities.
Another source of blunder is picking a coupling dependent on cost rather than performance necessities. Headed to decrease machinery costs, engineers may dupe the application by being excessively thrifty in their coupling decision.
While this methodology may reduce forthright component costs, extensive and expensive backend warranty guarantee claims can unleash ruin on an OEM’s primary concern and product reputation.
Another error is picking the wrong size: Choosing a coupling that is excessively substantial or unreasonably little for an application causes issues unfailingly. An engineer must know the powers and loads to which a coupling will be exposed.
Determine the best way to mount coupling to the shaft
The technique by which a coupling is mounted on the pole may decide the success or failure of that coupling, paying little respect to whether it is the right for the job.
Traditional keys, keyways, and decrease bushings function work well in unidirectional applications with minimal shock or turning loads. For reversing loads and shock applications, keyless locking gadgets are the favoured mounting method on the grounds that keyless gadgets are backlash-free.
For instance, mounting a torsionally rigid, backlash-free, high-speed disc coupling with a keyway and setscrew negates the backlash-free nature of that coupling. A keyless locking gadget would fill the coupling’s intended need better.
Then again, mounting an exceptionally adaptable jaw coupling with a keyless locking device could be pointless excess dependent on the unpleasant and adaptable nature of that coupling style.
Read More: Applications of Spider Star Jaw Couplings
Have the correct terminology
It might appear obvious, yet the units of the coupling’s torque rating are regularly confounded. Getting the spec wrong can make you miss the correct coupling decision by an excess of a request of extent.
Another area of confusion includes the utilization of keyways: Keyway couplings are for high torque, not high precision. In the event that the application requires turning around torques or course in addition to exact situating between the driving and driven shafts, keyways are improper.
Rather, a coupling with setscrew or clasp style hubs points is the best answer for accuracy applications. Numerous sorts of couplings, including adaptable bellows shaft couplings, allow no backlash, while others styles permit some backlash to happen.
Proper installation
Choosing the correct coupling for an application can be a complex procedure, however, need not be overly time-consuming. The best approach is to carefully think about all design criteria.
Commonly, these incorporate torque, shaft misalignment, firmness, rpm, inertia, space necessities, and shaft mounting. A coupling that tends to these issues will eventually execute as required in the application.
Realize that picking the right coupling isn’t the finish of the activity. It is similarly vital to introduce the coupling properly, checking that design contemplations were right.
Read More: What is Elastomeric Coupling?
An improper selection means the wrong type and wrong size
The most common mistake that engineers make while determining couplings and shafts is an improper choice, which incorporates choosing the wrong coupling sort and size.
Many coupling styles are accessible in the marketplace, and chances are that more than one sort of coupling will function admirably for a given application. On the other hand, there are likely numerous couplings that won’t function admirably for that same application.
Understanding application requirements and adjusting those against useful functional circumstances of available couplings will help identify the perfect product.
Read More: Role of high-performance turbine couplings in power plants
Difference between wrong and right
Perfect coupling choice is one in which the coupling is installed rapidly and after that overlooked for years and years. It is a coupling that does not flop because of application demands. Nor does it transfer stress or failure to mating segments. It doesn’t require booked downtime to maintain reliability.
The wrong coupling is the definite inverse and is typically simple to spot. It takes hours or days to introduce. It requires close flawless, tedious arrangement rehearses and requires to visit oil through booked downtime.
At the point when the wrong coupling comes up short, it regularly flops calamitously, all of a sudden, prompting broadened, spontaneous, expensive downtime.
Upon misalignment, the wrong coupling causes premature failure of mating equipment such as bearings, gears, or shafts. Rather than filling in like a fuse in the machine, the wrong coupling in an over-loaded machine exchanges transfers failure to increasingly costly parts, such as engines or gearboxes.
Proper coupling selection cannot be correctly made without a complete understanding of the misalignment being addressed in the system. Considering these tips can prove to be helpful in the application of coupling.
Lovejoy couplings are the leading and best manufacturer’s flexible couplings and spider star jaw couplings.