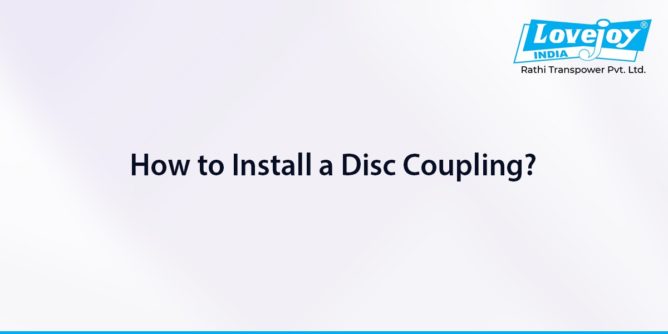
A disc coupling is a generally basic coupling design, comprising of two hubs, a centre member, two-disc packs and fastening equipment.
The following are a couple of tips that will help guarantee a proper disc coupling installation that will give long periods of solid and reliable service.
1) Safety and inspection
Before beginning, if it’s not too much trouble make a point to wear the correct personal protective equipment (PPE) and be sure lock-out tag-out methodology are pursued on stationary equipment to guarantee the system is securely segregated from all sources of potential energy.
Assess both the driving and the driven shaft, just as the hub point bores, to ensure they are free of dirt and burrs.
Clean and de-burr as important. Measure the bore and shaft diameters across to guarantee a legitimate fit.
On the off chance that the drag is tapered, check for good contact pattern, additionally guarantee the keys fit on the pole appropriately;
2) Mount the hubs
Install the key(s) in the shaft. In the hub is an interference fit bore, heat the hub in an oven to grow the bore adequately bigger than the shaft, 350°F is normally sufficient.
An open flame isn’t prescribed; however, if the main alternative, utilize an exceptionally huge rosebud tip to give even heating.
A thermal heat stick gives the most accurate proportion of hub temperature. With the hub expanded slide it on the shaft to the desired position.
Axial stops can be useful in getting a position set precisely. For freedom fit bores, make sure that the set screws the hub do not protrude into the keyway of the bore before installing.
Slide the hub up to the shaft until it is in the ideal hub position.
Fix the set screws to the torque worth appeared in the manufacturer’s installation guide.
Read More: Gear Couplings: Types and Applications
3) Check alignment
– Angular misalignment
Rigidly mount a dial marker on one hub and place the indicator on the face of the other hub.
Turn the two shafts together one revolution noting the minimum and maximum dial indicator readings.
The distinction of these qualities ought not to surpass the TIR worth indicated in the manufacturer’s installation guide.
– Parallel misalignment
Rigidly mount a dial indicator on one hub and place the indicator on the other hub flange outside diameter.
Turn the two shafts together one revolution taking note of least and greatest dial pointer readings.
The distinction of these qualities ought not to exceed the TIR value indicated in the manufacturer’s installation guide.
Read More: Applications of Spider Star Jaw Couplings
– Axial misalignment
The hub dividing of the centre points ought to be situated so the circle packs are level with no visual waviness.
The separation between the centre point faces that sandwich the circle packs should both be inside the cut-off points given for the “N” measurement in the producer’s installation guide.
4) Attach the centre member to the hubs
The centre part comes in a few arrangements. Depending on the coupling design you can have a part focus part, adapter mount centre member and non-adapter mount centre part.
The beneath technique spreads focus part mounting for the most present connector mount coupling arrangement: For adapter mounted focus individuals, the middle part sub-get together should be compacted to enable it to be dropped between the two directed centre points.
The middle part mounting capscrews is turn around introduced from the centre member side to compress the disc packs, in this manner shortening the general length of the centre member.
The disc packs ought to be compressed similarly on the two sides of the centre member and just enough so the inside part gets together will fit between the hubs.
After placing the compressed centre member between the hubs, the pressure capscrews can be relaxed to enable the inside part gathering to expand into the hub pilots.
Read More: What is Rigid Coupling and its Applications
5) Insert and fix the top screws
Compression capscrews are currently completely evacuated and embedded through the hubs and threaded into the centre member adapter holes.
Fix the top screw to the torque recorded in the manufacturer’s installation manual.
Re-check final alignment by again estimating the “N”. Measure at the 3, 6, 9 and 12 o’clock position for every one of the two plate packs.
The “N” measurement ought to be inside the range appeared in the manufacturer’s installation manual.
Rathi Couplings are the Best Coupling manufacturers in India. Rathi Couplings, a major coupling manufacturer with a history of successful implementations with designing and manufacturing custom disc couplings.
LoveJoy couplings are the major players in the coupling manufacturer delivering great products.